Why use a Hot Bolting Flange Clamp on a Depressurised Piping System?
- srjadmin
- Apr 16, 2024
- 2 min read
The BoltEx® hot bolting flange clamp can be used at full design pressure in an operating environment to exchange flange studbolts safely. BoltEx® has been designed to hold a flange together without loss of containment at 1.5 times the design pressure with all the flange bolts removed, and this has been proven across the range in a test environment. So, the question we seek to answer in this article is:
Why would you use a hot bolting flange clamp when exchanging flange studbolts on a depressurised piping system?

The question seems a little odd, as common thinking would be that if the flange is depressurised, why wouldn’t you change out the gasket and completely remake the joint? As often the case during a shutdown, the answer centres around time. In a shutdown, the focus is on completing tasks as efficiently and effectively as possible with zero margin for error.

Using a hot bolting flange clamp such as BoltEx® when changing the studbolts on a depressurised flange ensures that the gasket compression and positional integrity are not disturbed. Using a flange clamp means that there has been minimal movement of the flange faces or the gasket during the studbolt exchange; this means the chances of a leak path being introduced by the gasket being locally decompressed or disturbed are minimised.

A further reason for not breaking a flange when piping is depressurised is that the line would need to be drained and purged to make it safe, which adds time. So even when depressurised, the additional barrier in the form of a flange clamp guarantees that process fluids are contained, reducing risk to personnel by another level when exchanging the flange studbolts.
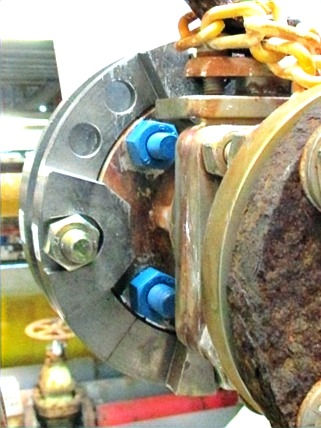
The reasons for requiring bolts to be exchanged are numerous, but when the gasket and flanges are in good condition, using a flange clamp to preserve that integrity even in a shutdown on a depressurised system can provide additional reassurance and pay significant dividends upon start-up.
Comments